A laser marking machine has complete marking tools, accessories, and high-tech inbuilt software and hardware programs. And, it is responsible for the precise, permanent, and accurate markings on metallic and non-metallic surfaces. In addition, we can do logo creations, barcodes, serial codes, designs, and many other operations in less time with few settings. First, we should understand here what is the marking principle of a laser marking machine. We shall be discussing it here, in brief, to understand it better.
How it works?
A laser marking machine has major components that decide its working phenomenon. And, it includes
- A laser system: A laser system includes CO2, Fiber, and a UV laser for more efficient results.
- Galnometer head and scanner: It is responsible for the Galvo settings to fix the beams on the specified area.
- Focussing lens: It reflects the beam emission on the material surfaces through the narrow spots.
- XY-axis rotating mirrors: These are two-dimensional axis rotational mirrors.
- Material(Metal and non-metal): It includes aluminum, copper, stainless steel, plastics, tiles, ceramics, and much more.
Below is the laser marking principle image for a better understanding:
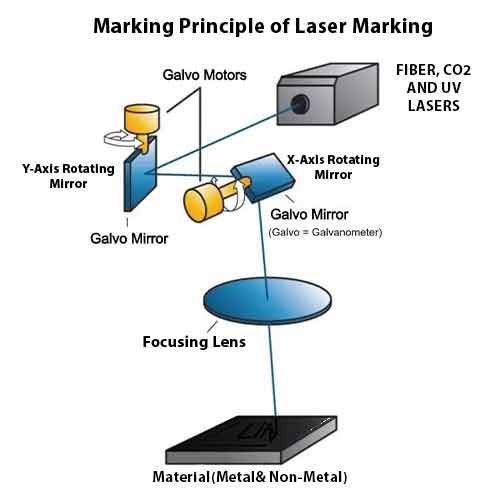
What is the laser marking principle?
The marking principle of laser marking involves using a laser beam to create permanent marks on a variety of materials(metallic and non-metallic). We can go through the below-listed points to get better clarity:
- Laser Generation: A laser beam is generated using a laser source. In addition, the type of laser used depends on the material being marked and the desired mark characteristics. Moreover, the commonly used lasers include fiber lasers, CO2 lasers, and UV lasers.
- Beam Manipulation: The laser beam quality depends on optical components such as mirrors, lenses, and galvanometer scanners. In addition, these components control the movement, focus, and intensity of the laser beam.
- Material Interaction: The laser beam that falls over the material leaves a fine mark. Afterward, the laser beam interacts with the material’s surface, causing different effects depending on the material and the laser parameters. So, all the listed below points describe it better:
- Ablation: In this process, the laser beam removes a thin layer of material from the surface, resulting in a mark. In addition, it includes the materials like metals, plastics, ceramics, tiles, glass, and much more.
- Melting: A laser beam melts the materials and creates a raised or depressed mark.
- Engraving: Laser engraving involves removing material through vaporization, resulting in deeper and more precise marks. This is commonly used for applications like serial numbers, barcodes, or intricate designs.
- Color Change: Certain materials, like metals or certain plastics, can undergo a color change when exposed to laser energy. This creates contrast or decorative marks and appealing designs on the material surfaces.
4. Control and Precision: Laser marking systems are highly controllable and precise. In addition, it allows appealing and intricate designs, fine details, and accurate markings. Further, there are many parameters, such as power, speed, pulse duration, and focus, that are responsible for the precision work. In addition, you can get the desired mark quality with proper adjustments.
Overall, the marking principle signifies the interaction between the laser beam and the material to create permanent marks. Moreover, the versatility, speed, and precision of laser marking make it widely used in various industries. Furthermore, you can go for product identification, traceability, branding, and customization.
How important is the marking precision in industry?
In many industrial applications like manufacturing divisions, packaging, food and beverages, and much more. Highly efficient and accurate markings over the material surfaces are important. So, that it could get brand awareness and prevent counterfeiting. Therefore, the laser systems like fiber, CO2, and UV lasers play an important role in laser marking. In addition, you can easily identify the products with their outside and permanent marks. This helps in marking logos, serial numbers, specifications, unique identification marks, and many others. So, here are some of the listed advantages and importance in industrial applications:
- Easy and fast production: Once, a laser machine is capable enough for precision markings, it does the fast marking works. And, it ultimately drives the production in industries in a limited timeframe.
- Enhances product branding: A good laser-marked product improves the branding of a material.
- Super-designing: Whether it is jewelry, woody furniture, metallic materials, utensils, or any other product. The super and appealing design of its surfaces attracts buyers.
- Cost-effective: Mass production reduces the costs and wastage due to its automation marking works.
- Environmental safety: Whether it is a safety protocol for the environment or the industrial atmosphere. The laser machines do not emit harmful gasses or wastages that can impact the environmental atmosphere.
Overall, by going through all the above info shared you can easily understand the laser marking machine principles. And, you can plan the marking needs and material categories as per your usability preferences. In case of getting more information, you can go through the laser machine’s specifications and do the proper settings. In case you are not sure about the laser marking efficiency and its working phenomenon with the required machine, you may connect us by Call or WhatsApp: 9804718718.