A laser marking machine works very efficiently and precisely for marking needs over non-metallic and metallic polished surfaces. However, many factors are responsible for the overall marking up to certain marking depths. So what are those parameters that justify the marking accuracy? We will be discussing here the entire adjustment needs of laser marking machines.
Machine’s Overview
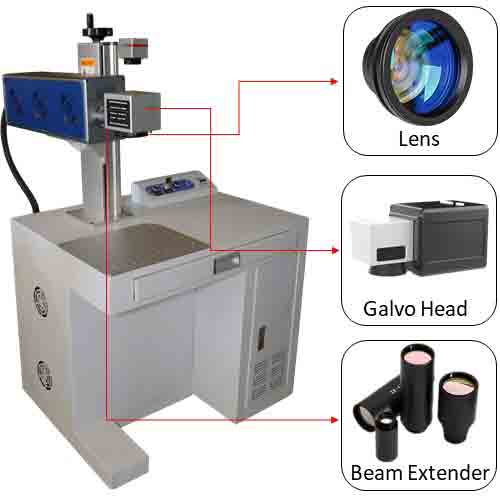
- Fiber-laser-marking-machine
- CO2-laser-marking-machine
- UV-lasermarking Machine
- MOPA-laser-marking-machine
- Starting Price-Rs.TBD+GST
- Call or Whatsapp: 9310620946
Main Component of Laser Marking Depth Controls
A laser marking machine marking depth control is decided based on accurate adjustments of the core components. However, you can also choose some basic laser-marking considerations before moving ahead. So, here are a few of the main components listed below:
- Q-Switched Pulses: Different power output of the machine is responsible for nanosecond light pulses creation.
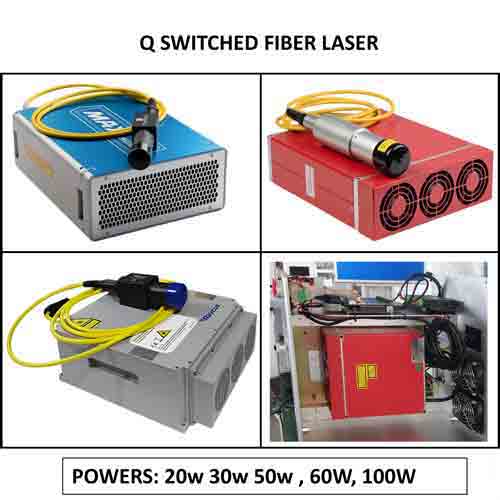
- F-Theta lens: It is used to focus the beam emissions and is made of high-quality optical materials.
- Galvo Head & Scanner: Galvo laser head uses a mirror for the light beam deflection. Here, we need a few adjustments as per the marking needs and material thickness and categories.
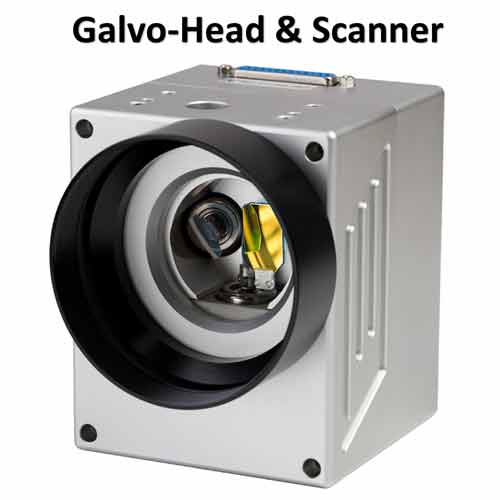
- Beam Extenders: You can prefix and adjust the laser beam diameter ratio using the beam extenders.
- Power Outputs: You can go ahead by using the correct machine’s output from 20W onwards for the better efficiency.
- Workbench Fittings: It is a work area that helps in fixing and holding the material tightly for further working operations of cutting, designing, markings, and engravings.
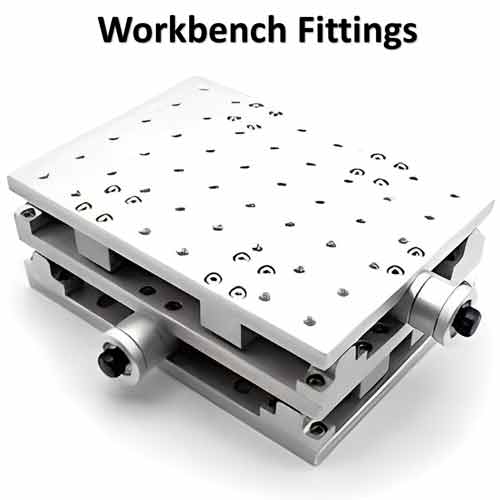
- Optical resonator: It helps in optical beam circulation via the closed beam areas and is of mainly two types first is a traveling wave resonator and the second is a standing wave resonator.
- Software and computer controls: All high-tech laser marking machine is Auto-CAD software operated. And control all the working operations using a computer control command.
How to adjust the marking depth of the material using laser marking?
A laser-marking machine has fixed tools responsible for the marking depth adjustments. To get the accuracy and precision of the marking depth over the material for laser marking, we need to do certain significant adjustments. And, here are the few listed:
- Laser Power Adjustments: For getting more clear, and denser beam quality, you can increase the laser powers and source.
- Marking speed of laser marking machine: You can get better results by adjusting the marking speed of the laser marking machine. You get denser marks at a slower marking speed and vice versa.
- Focal length and spot size visualization: By the appropriate adjustment of the focal length of the laser lens along with spot size. So, you can adjust the marking depth.
- Use appropriate laser accessories: By using the appropriate laser accessories you can expect better working efficiency and can also adjust the marking depth of the marking metallic and non-metallic materials.
Challenges and limitations of laser marking depth adjustments
Although, there are many benefits of marking depth adjustment using a laser marking machine. However, there are some challenges and limitations too. So, here we will go through some of those valid points:
- Material Compatibility: Different materials have different responses to laser marking, and adjusting the marking depth can be challenging based on the material composition. Moreover, certain materials may absorb or reflect laser energy differently, making it difficult to achieve consistent and controlled marking depths across various materials.
- Equipment Limitations: The laser marking equipment itself may have limitations in terms of its power, focus, or control settings. Additionly, these limitations can restrict the range of depth adjustments possible or make fine-tuning the marking depth challenging.
- Surface Variations: The material surface categories impacts the marking depth adjustments. In addition, uneven or curved surfaces may require additional adjustments to maintain consistent marking depths. Ensuring uniform depth on irregular surfaces can be technically demanding.
- Heat Distribution: Laser marking involves the localized heating of the material’s surface to create the desired mark. Adjusting the depth requires precise control of the laser power and exposure time to avoid excessive heat accumulation. Inadequate control may result in unwanted heat effects, such as material discoloration, melting, or damage.
- Cost Considerations: For implementing laser marking depth adjustments. It may require specialized equipment or additional features, increasing the overall cost of the marking system. It is important to weigh the benefits of depth control against the associated costs and determine the optimal balance for specific applications.
Addressing these challenges and limitations often involves a combination of expertise, experimentation, and advanced laser marking systems. In addition, knowledgeable suppliers or manufacturers of laser marking equipment can help overcome these limitations. Further, it helps to achieve the desired marking depth adjustments for specific materials and applications.
Finally, after going through all the parameters of the marking depth adjustment factors, its challenges, and limitation. We have come to the point that everything needs to get handled precisely. In addition, material category, thickness, power output, and other requirements need to get proper fixing before any move. For, further clarification and a better understanding of the correct laser marking machine, you can connect us Call/Whatsapp: 9212300300.